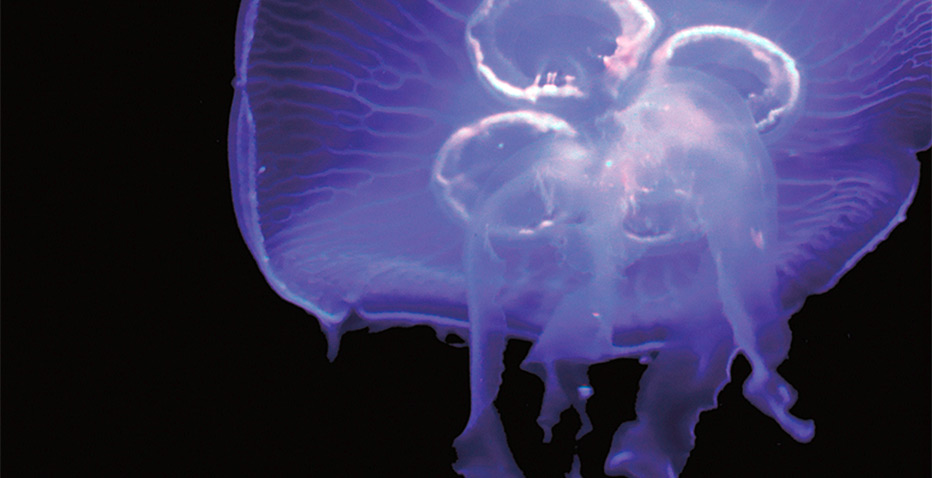
Deep sea electrical current monitoring
- Product range:
- Control
MENCK GmbH, with its headquarters in Kaltenkirchen, has produced steam boilers, winches and pile driving hammers for the offshore industry for more than 140 years. The company's continuously developed products are used in oil, gas and wind farm projects, as well as for the construction of bridges and harbours. In order to achieve increased functionality and operating safety, the company had the control of the MHM hydraulic hammer modernised. Because the hydraulic hammer is used at underwater depths of 1800 to 3000 meters, particular demands are placed on the control computer as well as its pressure-resistant container and the cables used. The MUX-Box comprises of the pile driving hammer control computer and the deepwater system hydraulic power pack. It communicates via DSL with the PC-based operating computer in order to change the process image. Furthermore, it ensures that the solenoid valves for actuation of the hydraulics work reliably, and that water penetration does not lead to a total failure of the device. In collaboration with Friedrich Lütze GmbH and the systems house ESD electronic system design, an unconventional solution to the task was found.
New control makes construction easier
The new control computer by ESD, previously a 68000 processor in the VMEbus system, has now been realised with PowerPC on the CompactPCI-Bus and CANopen communication. Several RS485 interfaces have been replaced through redundant DSL lines (in total up to 5 Mbit/s). The computer features eight serial interfaces and a CANopen CBX-I/Os for 32 analogue inputs, which integrates devices such as a compass, a depth pressure sensor and an acceleration sensor (gyro). In addition, it has 16 PT100 inputs for recording the conductivity as well as diverse temperatures, the results of which can be used to determine water penetration, water pressure, oil temperature or the water proportion in oil. The control also provides 64 digital inputs and outputs as well as two Ethernet interfaces. The extremely compact computer is part of the MHC 21 control and monitoring system, and has been integrated into the MUX-Box, which is installed directly on the hammer. This arrangement means that only one single cable with power and DSL lines and the air supply is required for operation at depth.
Electronic Solid State Relay with integrated overload and short circuit protection
With the reconstruction of the control computer, the solenoid valves of the hydraulic hammer are to be switched, in future, via electronic relays. In addition, those responsible requested from MENCK an integrated current measurement so that the flow of current through the solenoid coils can be checked. The current paths were also required to have a redundant design. The background to these requests are the high offshore costs if the device has to be pulled onto the deck of the special ship due to a defect. "At daily rates of more than 500 thousand dollars for the ship, every minute in which a device remains inoperable counts", explained Rainer Kropf, Electrical Engineer at MENCK. The intelligent LOCC-Box power monitoring system by LÜTZE already provides the most important characteristics. The modules provide reliable protection by DC 24 V circuits up to 10 A. The current range is adjustable in 1 A steps, as is the selection of the characteristics (fast-blow, medium time-lag and slow-blow 1, 2 and 3). The additional components LOCC-Box-GW (gateway) permit communication with the control via CANopen. The modular system can also be extended at any time. For this application, LÜTZE developed a special firmware, so that the LOCC-Box system behaves like a fused power circuit-breaker (Solid State Relay) and the fuse function is reversible. "We pursued various solution approaches; an adaptation of the firmware was the most obvious and also the most inexpensive solution", said Klaus Wünschirs, Product Market Manager Automation at LÜTZE. MENCK themselves created the appropriate safety concept. It takes into account the redundant construction with eight LOCC-Box-Net modules on one LOCC-Box- Gateway, as well as Namur isolation amplifiers in the signal circuit of the proximity switch, which are installed together in a 3HE plug-in unit of the MUX-Box.
Operationally safe through condition monitoring
In order to obtain knowledge of the module status and the condition of the solenoid valves, ESD developed a customer-tailored application using the network-capable LOCC-Box gateways and a CAN bridge, which takes on condition monitoring functions. Here the gateway functions as the LOCC-Box master, and communicates via the LOCC-bus based on LIN (Local Interconnect Network). In this way, the current and voltage values for each LOCC-Box net can be queried from the control station, and a comprehensive diagnosis can be carried out together with the queried module status. In addition, the user can shut down the defective path from the control station in case of short circuit or overload, and deactivate the module conditions, short circuit or triggered. Therefore, if a connection no longer functions, for example due to water penetration, the redundant LOCC-Box net module is activated, meaning that it is possible to continue work without any delays. The individual paths with logged current and voltage values permit the user to determine the technical condition of the connected consumers, so that appropriate measures can be conducted in good time to avoid functional failure at depth.
Summary
The concept of the reversible line protection is particularly pertinent for deepwater systems (oil drilling, deep sea foundations). Electronic Solid State Relays are not subject to mechanical wear, meaning that they can undertake far more switching procedures over their lifetime. Based on the intelligent LOCC-Box power monitoring system by LÜTZE, ESD developed a customer-tailored application which also caters for conditioning monitoring functions. With the firmware by Lütze, the LOCC-Box acts like a fused 10 A power circuit-breaker.